Пробиването на отвори е вид металообработка с помощта на въртящи се инструменти с метод на рязане. Тази операция е разделена на дълбоко пробиване и конвенционално. В първото изпълнение дълбочината на отвора е повече от 10 cm или има размер от повече от 5 налични диаметъра (d * 5). Пробивите се оказват, че се получават канали с различна дълбочина и диаметър (с няколко напречни сечения).
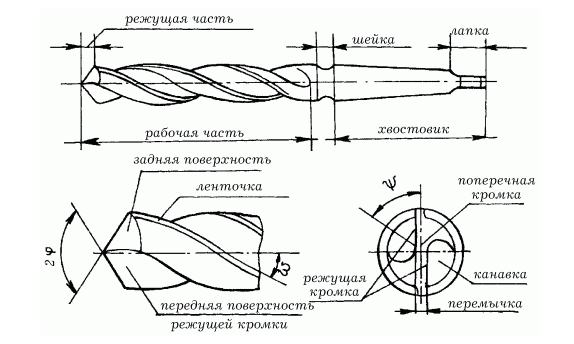
Схема на свредло метала.
Пробиването на отвори в метала е възможно по един от следните начини:
- Извършете въртенето на детайла и в същото време изработете надлъжния не-въртящ се инструмент за пробиване.
- Въртенето на детайла не се извършва, то се заема фиксирана позиция.
- Еднократно движение около оста и механизъм и детайли.
На практика тези технологии са доста популярни. Процесът на оформяне на дълбоки дупки се търси в области като производство на тръби, металургия, космическа и нефтена и газова промишленост, производство на топлообменни плочи и др. метални черупки и др.
Дълбоко пробиване на дупки: класификация
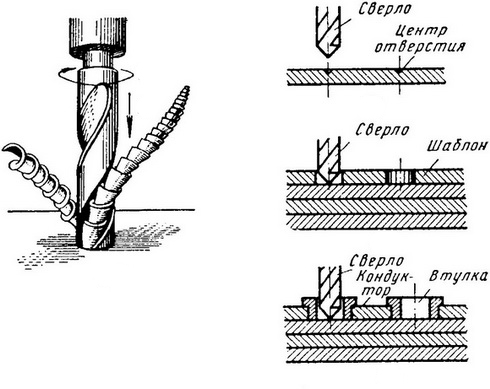
Схемата на пробиване на метал.
- От вида на изваденото съдържание (чипс) излъчват: пръстен и непрекъсната процедура. При втория метод, пробитото съдържание се показва като частици на частици, при първия метод пръстеновидната равнина се отстранява частично като пръчка, а другата част се отстранява с чипове.
- Според метода на рязане излъчва технология:
Однощанговая (STS). Този метод е оптимален за производството на заготовки в процес с висока производителност или масово производство. Проблемът тук е, че трябва да използвате маслоприемник с различни захранващи маркучи, като едновременно с това въртите детайла. Тази система е призната за най-ефективна при формирането на висококачествени дупки.
Изхвърлям. Опция за дълбока обработка с параметрите на продукти със средно качество. Обработката се извършва на стругове с различни сложни функции. Системата включва използването на допълнителна мобилна или инсталирана помпена станция. Този метод позволява да се получат отвори с диаметър от 2 до 6 см в дълбочина до 120 см, включително периодично.
Пистолети (тръбни остриета) със свръхзахранване от вътрешната страна. Този вариант е подходящ за малки предприятия, в които условията на технологията планират да произвеждат отвори с малък диаметър.
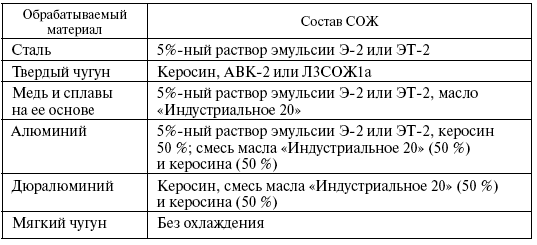
Избор на таблица на охлаждаща течност при пробиване на различни видове метал.
Свредла с единичен нож лесно се вграждат в универсалния принцип на действие на машината. Фрезата е изработена от твърди сплави и има V-образен жлеб в сърцевината. Ъгълът на пречупване на последния може да достигне 110-1200º. Препоръчителният диаметър за пробиване е 3, 5-4, 0 cm, дължина - d * 50. Този метод не позволява операциите по разгръщане и разгъване.
Автоматичният контрол на процеса ви позволява да изберете: дълбоко въздействие с автоматична промяна на един или много работни параметри (захранване с масло, скорост на въртене и др.).
Характеристики на процеса на дълбоко пробиване
При дълбока обработка се следват основните принципи на технологичния процес.
Първоначално се извършва избор на скоростта на въртене на сондажното оборудване или на максималната възможна скорост на рязане (бургии за подаване).
Наблюдавайте осигуряването на нормалното раздробяване на стружките, изцяло изтеглянето на съдържанието на вдлъбнатините.
Важен нюанс в момента на изрязване на отпадъците е ножът за инструмента за безопасност. В тази част на тренировката не трябва да има повреди, както и закъснения и други недостатъци. Друг ключов критерий за ефективното третиране на металните повърхности е снабдяването с охлаждаща и смазочна течност съгласно правилата.
Тъй като частите са пробити, придружени от подаване на охлаждаща и смазваща течност с определено налягане и предварително зададен дебит, работата на помпените устройства - маслени помпи или помпи за изпомпване на вискозни вещества - се въвежда в системата.
Мощността на системата се избира на базата на разхода на флуид и необходимото количество налягане за подаване на смазка.
Доставката на флуиди е незаменима технологична точка:
- Правилното извеждане на чип от работната зона се извършва чрез оловни канали.
- Силата на триене между контактните елементи е намалена.
- Излишната топлина, генерирана по време на дългия процес на пробиване, се премахва, докато свредлото се запазва.
- Допълнителна обработка на изкопа.
Някои трудности на процеса
С увеличаване на дълбочината има повече трудности при изкопаването.
При дълбоко пробиване се използва специализиран инструмент, който е технически оборудван с допълнителни възможности за използване на режещи и други видове устройства. Това е необходимо поради факта, че използването на стандартни инструменти не позволява да се постигне висока производителност на процеса и понякога го прави невъзможно.