Хладилните устройства се различават от останалите основни уреди за битови уреди, докато функционират ежедневно. Те обаче подлежат на счупване.
При чести капки напрежение на захранващата мрежа, компресорът за хладилника първо се проваля. Именно този механизъм се счита за най-важния елемент на системата, която задвижва фреоновите тръби, поради което се осигурява охлаждане.
В тази статия разглеждаме съществуващите видове компресори и анализираме причините за типичните аварии. Също така даваме подробна инструкция как да я замените сами.
Съществуващи типове компресори
Разбивка на най-важния елемент на хладилника най-често се случва в резултат на токови удари. Ако редовно имате проблеми с електричеството, препоръчваме да погледнете регулаторите на напрежението.
Счупен компресор обещава значителни разходи не само за закупуване на ново устройство, но и за работата на капитана.
Въпреки това, можете да отидете в друга посока и да направите своя собствена подмяна. Който и вариант да бъде избран, първата стъпка е да се намери правилния тип компресор.
Въздуходувка за колектор
Получавайки информация за иновативни модели хладилници от източници, можете да попаднете на такова нещо като „нормален” компресор. Но не всеки знае значението му.
Този термин се отнася до колекторния механизъм с вертикално монтиран вал на електродвигателя. Монтира се върху пружинен механизъм и затворена запечатана кутия, като по този начин осигурява висока степен на звукоизолация.
При по-старите модели е използвана хоризонталната подредба, която прави устройството по-шумно - вибрациите се отразяват върху цялото тяло.
Той използва стандартния принцип на работа и технологията, разработен преди много десетилетия - вентилаторът работи до достигане на зададения температурен режим в хладилния агрегат и след това се изключва.
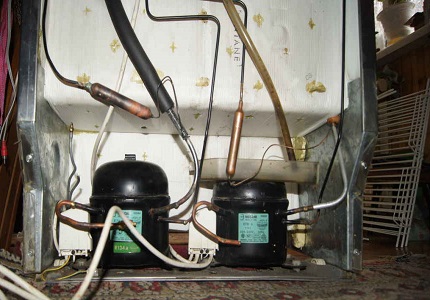
Моделите на изследването са оборудвани с предимно бюджетни версии на хладилници и това е единственото им предимство пред другите представители на вида.
Компресор тип инвертор
Модернизираните устройства са оборудвани с инверторен компресор. Един обикновен компресор отива на върха на възможностите си, когато е изключен, и има много такива повторения в деня, и съответно, той е обект на бързо износване и намален експлоатационен живот.
Докато инверторните устройства работят дори и при достатъчно инжектиране на въздух в камерите, периодично намаляват броя на оборотите. Устойчивостта на съставните елементи е много по-ниска и съответно периодът на непрекъсната употреба е по-висок.
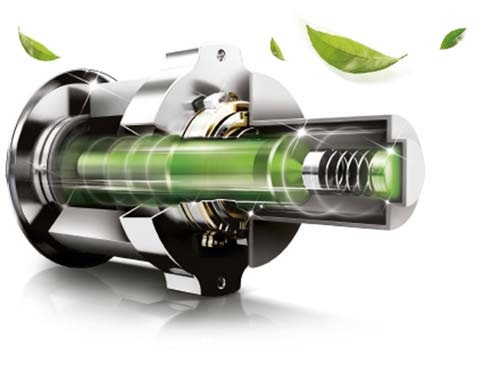
Водещите позиции в разработването на инверторни устройства са взети от Samsung, който първи е масово оборудвал хладилници с не-превключващи механизми. Производителите дават десетгодишна гаранция за работата си.
За да научите повече за характеристиките на хладилниците с инверторен компресор, техните предимства и недостатъци, моля следвайте тази връзка.
Линеен изглед на устройството
Иновационното развитие на внесените технологии включваше нов тип компресори - линейни. Принципът на действие е подобен на предишните версии на устройствата, но този тип функции е много по-тих и по-икономичен.
За разлика от конвенционалните механизми, няма колянов вал. Чрез действието на електромагнитните сили се осигурява от възвратно-постъпателно движение на ротора.
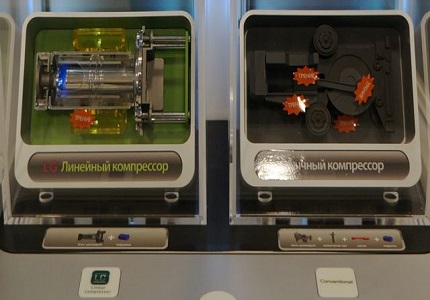
Линейните вентилатори са технически сходни с предишните два аналога, но имат няколко съществени предимства:
- по-малко тегло;
- висока степен на надеждност при работа;
- липса на триене в равнината на компресия;
- приложение при условия на ниска температура.
LG се смята за главния идеолог, който е започнал активно да прилага линейни компресори. Най-често те се използват в хладилници със система No Frost, които имат отделни регулатори на температурата в различни единици.
Ротационен вентилатор с плочи
Ротационните (ротационни) хоризонтално или вертикално разположени вентилатори са оборудвани с един или два ротора и са аналози на двувинтов сокоизстисквач, но спираловидните спирали са неравномерни.
В зависимост от принципа на работа, те се разделят на два основни класа: с вал и въртящ се вал.
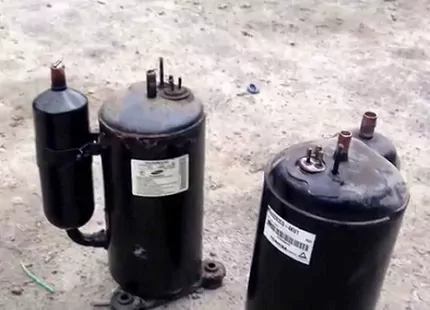
В първия случай единицата е представена от двигателен вал с монтиран цилиндричен бутало, което е ексцентрично около центъра, т.е. е изместено.
Върху корпуса на цилиндъра се извършват завъртания. Разстоянието между корпуса и ротора променя размерите си по време на въртене.
На мястото на минималния отвор има инжекционна дюза, максималната - всмукване. Към циркулационното бутало се прикрепя на свой ред плоча посредством пружина, която блокира пространството между двете дюзи.
Във втория вариант принципът на действие е подобен с една разлика: плочите са фиксирани и поставени на ротора. По време на работа буталото се върти спрямо цилиндъра и плочите се въртят заедно с него.
Общият алгоритъм на хладилника
Работата на всички хладилници се основава на излагане на фреон, който действа като хладилен агент. Придвижвайки се около затворения контур, веществото променя показанията на температурата.
Под налягане хладилният агент се довежда до кипене, което е от -30 ° С до -150 ° С. Изпарява се, улавя топлата атмосфера, разположена по стените на изпарителя. В резултат температурата в хладилния агрегат се понижава до предварително определено ниво.
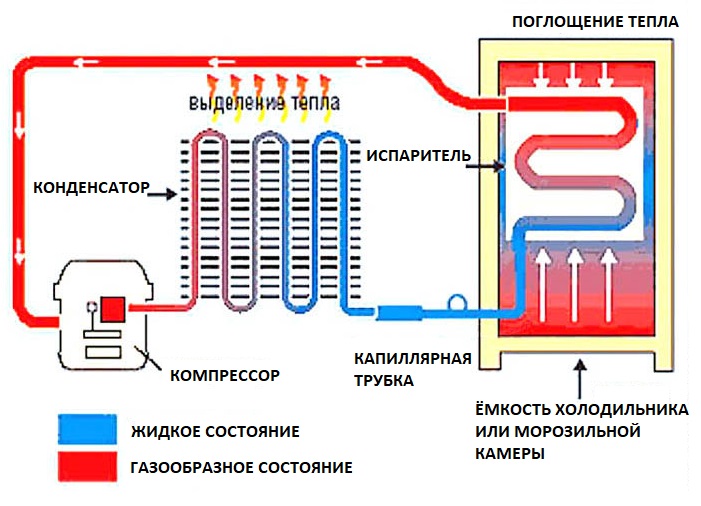
В допълнение към основното устройство под налягане, което създава налягане в хладилника, има допълнителни елементи, които изпълняват посочените опции:
- изпарител, който събира топлината вътре в хладилния агрегат;
- кондензатора, който отклонява охлаждащата течност;
- дроселиращо устройство, което контролира потока на хладилния агент през капилярна тръба и термостатичен вентил.
Всички тези процеси са динамични. Трябва също така да вземем предвид алгоритъма на двигателя и принципа на работа, когато той се повреди.
Компресорът е отговорен за системното регулиране на спада на налягането. Изпареният хладилен агент се вкарва в него, който се компресира и избутва обратно в топлообменника.
В същото време се повишават температурните показатели на фреона, поради което става течен. Компресорът работи с помощта на електрически мотор, разположен в запечатан корпус.
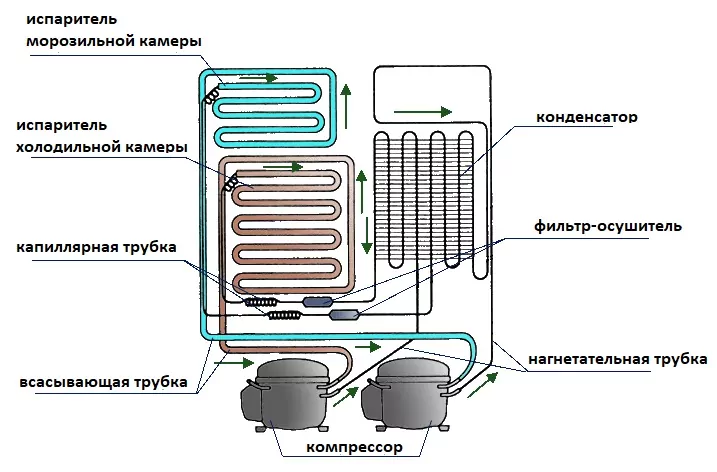
Освен това си струва да се отбележи, че повечето хладилни устройства имат различни температурни индикатори вътре в основното устройство. Така производителите опростяват системата за организиране на съхранението на различни категории продукти.
В зависимост от зоната, климатът може да се регулира от сухо до мокро, а температурата на основното отделение е от 0 до 5-6 ° C, а температурата на фризера - до -30 ° C.
По-подробно устройството и принципът на работа на хладилника са разглобени в тази публикация.
След като се заемете с устройството, преминете към анализа на основните фактори за отказ на компресора, след което ще трябва да го демонтирате.
Основните причини за отказ на компресора
Всички проблеми в компресионния възел са условно разделени на две основни групи: с работещ и неработен двигател. Първият вариант е следният: когато включите, можете да чуете звука от компресора, светлината на хладилника е включена. Съответно, в друго изпълнение - устройството изобщо не се включва.
Причина # 1 - изтичане на хладилен агент или дефект на термостат
Тук основната причина може да бъде изтичането на фреон.
Можете да извършите самотест по този начин: докоснете кондензатора - неговата температура ще съответства на стайната температура.
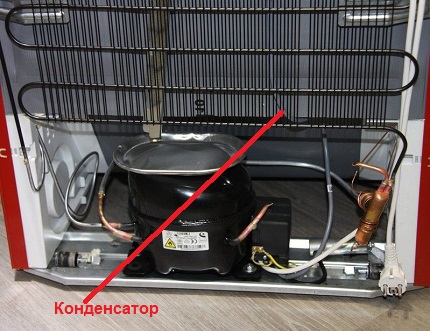
Възможна е и друга причина - отказът на термостата. В този случай сигналът за грешен температурен режим просто няма да бъде получен.
Причина # 2 - проблеми с навиването
Ако уредът не се включи, възможна причина може да бъде отворена верига на намотките на компресора.
Такава ситуация може да се случи както на работното място, така и при стартиране или на две наведнъж. Когато хладилникът е включен, вентилаторът не работи, а температурата на устройството е стайна температура.
Причина # 3 - затваряне с преплитане
Устройството започва, но не повече от минута. И тялото е прегряване.
В този случай, намотките на намотката са затворени, тяхната съпротива е намалена и увеличеното напрежение преминава през релейния блок. Релето изключва компресора, ще се чуе щракване. След охлаждане на стартера, той отново включва компресора и т.н. в кръг.
Причина # 4 - изземване на двигателя
При включване се чува електрически мотор, но въртенето не се извършва, компресорът не се свива, съпротивлението на намотките е максимално.
Причина # 5 - отказ на вентила
Загуба на охлаждаща мощност поради дефекти на клапаните.
В резултат на такава повреда, уредът работи без изключване и не създава подходящо ниво на компресия, съответно, единиците на хладилното устройство не достигат желаната температура.
Често в такъв случай може да се чуе нехарактерно звънене на метални части по време на работа. Можете да разберете това чрез определяне на степента на подаване на въздух.
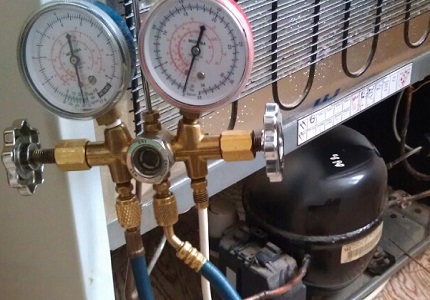
За да проверите “диагнозата”, трябва да отрежете накрайника за пълнене с помощта на нож за тръби. Подобни действия се извършват с кондензационен филтър.
Сега, на тяхно място, свързваме манометричния колектор, включваме вентилатора и проверяваме генерираното ниво на компресия на въздуха - нормата е 30 атм.
Причина # 6 - Термичен сензор или реле за стартиране
Необходимо е също така да се проверят за дефекти такива елементи като термостатичния датчик и стартовото реле.
При тази повреда компресорът не се включва или включва за 1-2 минути. При проверка на съпротивлението на намотките се записват номиналните стойности.
Процес на поетапно самозамяна
Ако причините за неизправностите не са идентифицирани, самият вентилатор трябва да се поправи. А за да я стартирате, ще трябва да се отстрани от хладилния агрегат и да се тества.
Етап # 1 - демонтиране на компресора
Компресорът се намира зад хладилника в долната му част.
В процеса на демонтиране ще бъдат приложени следните инструменти:
- клещи;
- ключове;
- плюс и минус отвертки.
Между две връзки, свързани към охладителната система, е поставен компресор. С помощта на клещи трябва да хапят.
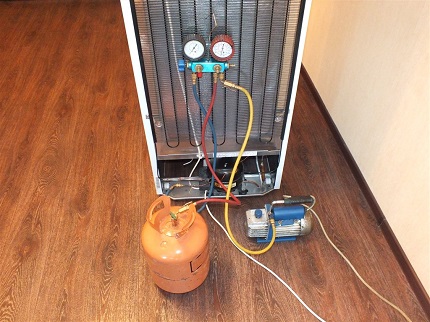
Хладилникът се стартира за 5 минути, през които фреонът преминава в състояние на кондензация. След това към линията за пълнене е свързан вентил с маркуч, свързан към цилиндъра. След 30 секунди, когато клапанът се отвори, ще се обезвъздуши целият хладилен агент.
След като премахнем релейния блок. Визуално, тя може да бъде сравнена с обичайната черна кутия с излизащи от нея жици.
На първо място, стартерът маркира горната и долната част - това е полезно в процеса на повторно инсталиране. Отвиване на скобите и изваждане от траверса, също и закуска на кабелите, водещи към щепсела.
Всички скрепителни елементи са усукани заедно с устройство за наблюдение. Почистваме всички тръби за запояване на ново устройство.
Етап # 2 - измерва съпротивлението с омметър
За да проверим функционирането на компонента, ще извършим външна проверка, както и тестване и проверка на отделните му компоненти. Първо проверяваме състоянието на двигателя. Това може да се направи с помощта на мултиметър или омметър.
Както бе споменато по-рано, захранващият кабел първоначално се проверява. Ако той е работник, ние разглеждаме самия компресор. За да направите това, използвайте тестера.
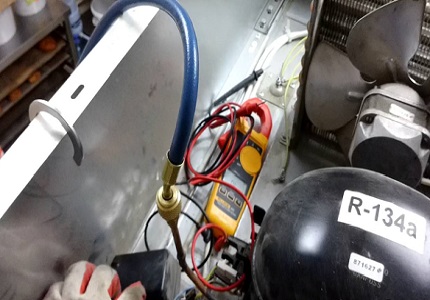
Преди всичко, свалете защитното устройство и премахнете съдържанието, изключете от стартовото реле. След това с помощта на мултицетните сонди измерваме жиците по двойки.
Сравняваме резултатите с таблицата, която показва оптималната производителност на конкретния модел компресор.
Данните на работещо устройство в стандартната версия ще бъдат следните: между горния и левия контакт - 20 ома, горната и дясната - 15 ома, лявата и дясната - 30 ома. Всякакви аномалии показват сривове.
Проверява се съпротивлението между захранващите контакти и корпуса. Индикациите за прекъсване (знак за безкрайност) показват, че уредът е в добро състояние. Ако тестерът дава някакви индикатори, най-често е нула - има неизправности.
Етап # 3 - проверете силата на тока
След проверка на съпротивлението е необходимо да се измери тока. За тази цел свържете стартовото реле и включете електродвигателя. Кърти тестера, за да закрепи един от мрежовите контакти, водещи към устройството.
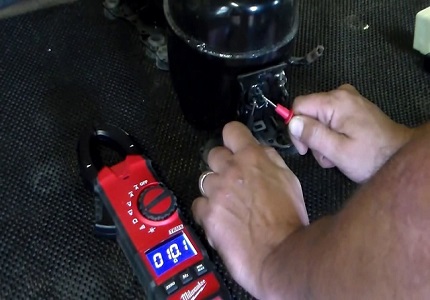
Токът трябва да бъде идентичен с мощността на двигателя. Например, 120 W двигател съответства на ток от 1.1-1.2 А.
Етап 4 - подготвяме инструменти и оборудване
За да замените дефектен хладилен компресор, трябва да подготвите следния набор от инструменти и материали:
- преносима станция за регенерация, зареждане с гориво и евакуация;
- заваръчна машина или горелка с газов MARR балон;
- Компактен нож за тръби;
- акари;
- Съединител Hansen за херметично свързване на компресора с пълнещата дюза;
- медна тръба 6 mm;
- филтър абсорбер за инсталиране на входа на капилярната тръба;
- медни сплави с фосфор (4-9%);
- приспособление за запояване;
- цилиндър с фреон.
Трябва да се съсредоточите и върху мерките за безопасност при работа с ремонтно оборудване. На първо място, трябва да оборудвате изолиращата платформа и да изключвате охлаждащото устройство от електрозахранването.
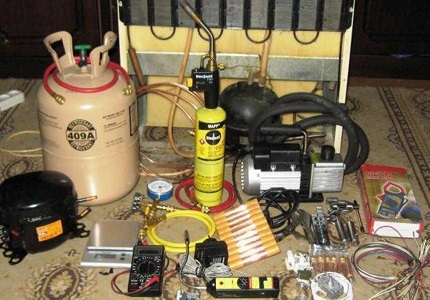
След всяко пълнене с фреон, преди запояване стаята се вентилира за четвърт час. Не се допуска включване на отоплителните уреди в помещението, където се извършват ремонти.
Етап # 5 - монтираме нов компресор
Първата стъпка е да се прикачи нов компресор към траверса на хладилния агрегат. Извадете всички щепсели от тръбите, идващи от компресора и проверете налягането на атмосферата в устройството.
Не го поставяйте в налягане преди 5 минути преди запояването. След това извършваме скачване на компресорните дюзи с линиите за изпускане, засмукване и пълнене, дължината им е 60 мм, а диаметърът е 6 мм.
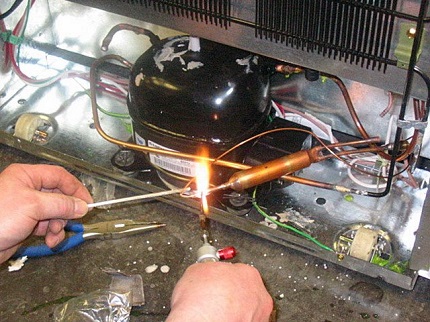
Процесът на запояване тръби се извършва в съответствие с последователността: зареждане, разреждане на излишния хладилен агент и инжектиране.
Сега изваждаме щепселите от филтърния сушител и го монтираме на топлообменника, като вкарваме дроселната тръба в него. Запечатваме шевовете на двата контурни елемента. На този етап поставяме съединител Hansen на маркуча за пълнене.
Етап # 6 - стартираме хладилния агент в системата
За пълнене на хладилната система с фреон, свързваме вакуум към пълначната линия с съединител. При първоначално пускане се довежда до налягане от 65 Pa. Установив на компрессор защитное реле, производится коммутация контактов.
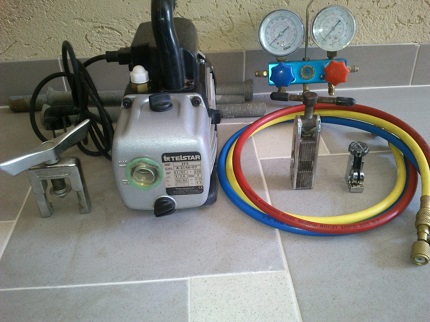
Подключить холодильник к электропитанию и заполнить хладагентом на 40% от нормы. Это значение указывается в таблице, расположенной сзади устройства.
Агрегат включается на 5 минут и проверяются соединительные узлы на предмет герметичности. Затем его нужно снова отключить от питания.
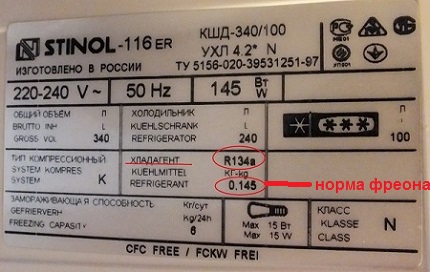
Выполнить второй раз вакуумирование до остаточного значения в 10 Па. Длительность процедуры не меньше 20 минут.
Включить агрегат и произвести полное заполнение контура фреоном. На финишном этапе консервируем трубку методом пережатия. Снимаем муфту и запаиваем патрубок.
Если вы никогда не занимались подобными работами, рекомендуем более подробно изучить процесс самостоятельной заправки холодильника фреоном.
Полезные рекомендации по пайке швов
Пайка двух патрубков, произведенных из меди, осуществляется сплавом меди с фосфором (4-9%). Состыкованные элементы размещают между горелкой и экраном, разогрев его до вишневого цвета.
Накаленный припой опускают во флюс и расплавляют нажатием прутка к нагретому стыковочному участку.
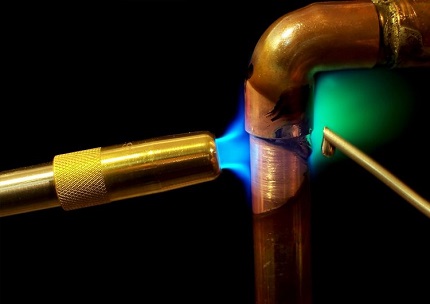
Для пайки трубок из стали или из его сплава с медью применяется припой с содержанием серебра. Паяльный элемент подогревают до красного цвета.
После того как шов затвердел, его протирают влажной ветошью для устранения флюсовых остатков.
Заключения и полезно видео по темата
Инструменты и материалы, что потребуются для замены компрессора, а также все этапы работы доступно изложены в видеосюжете на примере холодильника Атлант:
Основные правила вакуумирования и перезаправки охладительной системы:
Заявленный производителями срок службы компрессора составляет 10 лет. Однако и его поломки неизбежны.
В случае неисправности нагнетателя можно заменить сломанный компрессор самостоятельно, предварительно ознакомившись со всеми правилами безопасности и этапами предстоящей работы. Также для этих целей предстоит запастись необходимым оборудованием .
Профессионально занимаетесь ремонтом холодильников и хотите дополнить приведенный выше список причин поломки компрессора? Или поделиться с новичками полезными советами по ремонту? Пишите свои замечания и рекомендации внизу под этой статьей.
Если у вас остались вопросы по самостоятельному устранению поломок, задавайте их нашим экспертам в комментариях к этой публикации.