Заваряването на метали се появява с появата на коване. Появата на все по-сложни механизми изисква подобряването на процесите на коване и заваряване. Свързването на отделни части към твърди ковашки единици е сложен и отнемащ много време процес, но преди появата на заваряване с електрическа дъга е единственият възможен.
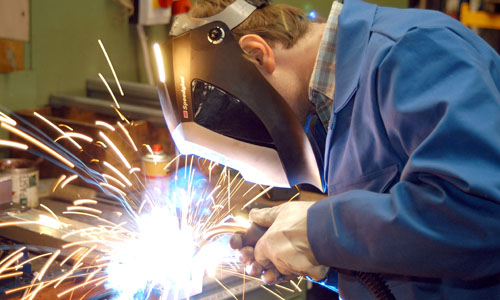
Заваряването е най-лесният и най-траен начин за свързване на различни метални части.
Понастоящем са разработени повече от 150 метода на електродъгово заваряване, а развитието на новите технологии продължава.
Основни видове заварки
Сегмент на съединение, образуван в резултат на процеса на кристализация на стопен метал, се нарича заварка. Една от основните характеристики на заваръчните съединения е заваръчната крака.
Има два вида заварки (да не се бърка със заваръчния шев):
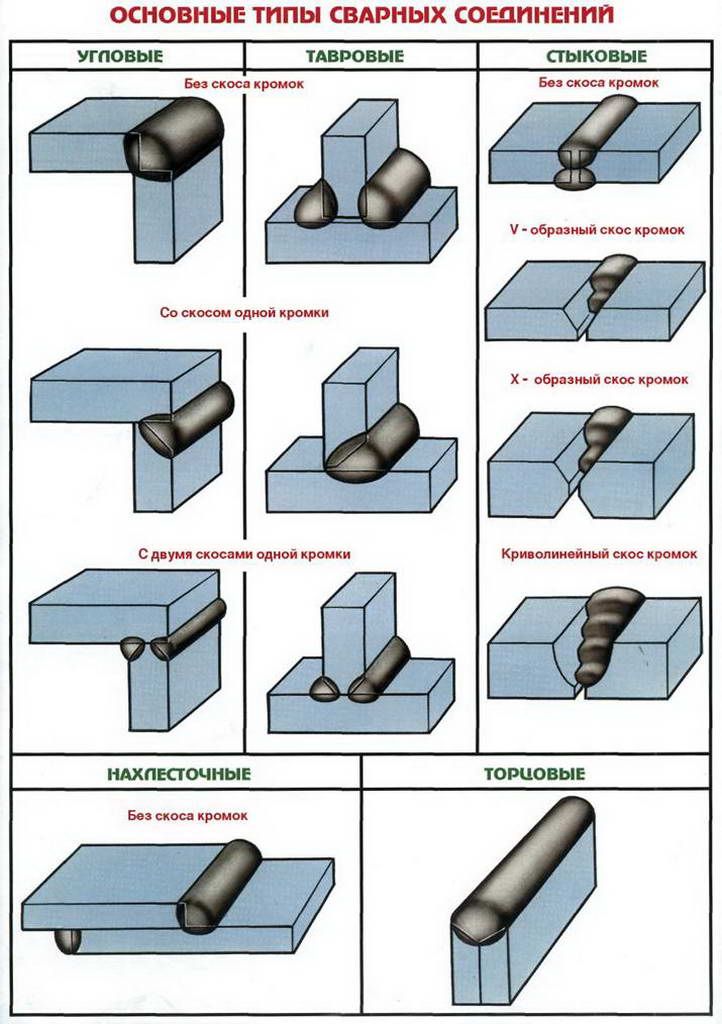
Основните видове заварени съединения.
- Заварена заварка: използва се за съединяване на челни съединения, т.е. части са свързани крайни ръбове. Втулката се извършва без режещи ръбове, с изрязани и изгорени части. Ръбовете могат да имат криволинейна форма, V-образна и Х-образна форма. Листове до 8 мм могат да бъдат заварени без режещи ръбове, но листите трябва да бъдат положени с разстояние до 2 мм. На практика, примките са по-често използвани за свързване на тръбопроводи и при производството на конструкции от листови метали. Такива съединения са най-икономичните и по-малко консумиращи енергия.
- Ъгъл: всъщност са ъглови, Т-образни и припокрити. Ръбовете могат да бъдат едностранни и двустранни, в зависимост от дебелината на метала. Ъгълът на рязане се избира от 20 ° до 60 °. Все пак, имайте предвид, че по-голям ъгъл на рязане изисква повече метал за пълнене, което означава, че производителността и качеството са намалени.
- Електрическото заваряване се използва за покриване на големи метални конструкции. Използва се, например, в производството на пътнически автомобили, когато използването на твърди фуги е трудно и нерентабилно. Електро-клепаните фуги са доста силни, но не и плътни.
Обикновено заваряването се извършва наведнъж, но ако дебелината на заварения метал не позволява да се свари материала, той се извършва в няколко преминавания. Този метод се нарича многослоен. В този случай, всеки предходен слой впоследствие се отгрява, в резултат на тази топлинна обработка, свойствата и структурата на шва се подобряват значително.
Необходимо е да се избере вида на връзката в зависимост от конфигурацията на изпълнявания елемент. Крайният продукт трябва да работи, да прехвърля проектното натоварване и да не се поддава на повреда от умора.
Предимства на заваръчните съединения:
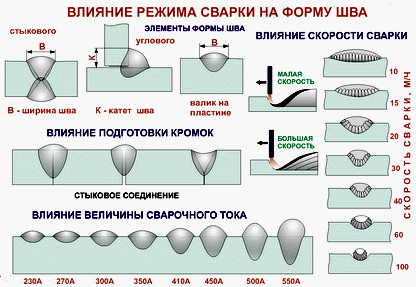
Влиянието на режима на заваряване върху формата на шва.
- Ниска сложност и лекота на свързване.
- Малък, в сравнение с други видове връзки, шумът на процеса.
- Можете лесно да автоматизирате процеса.
Недостатъците включват възможността за остатъчни напрежения и ненадеждността на работа при вибрации и ударни натоварвания.
Свойства и геометрия на заваръчните шевове
Във всички проекти има работни шевове, които възприемат основните натоварвания. Изчисленията за якост на работните шевове се извършват при пълен товар плюс 25%. Свързващите шевове се използват за свързване на отделни елементи - изискванията към тях не са толкова твърди, тъй като в случай на унищожаване, експлоатацията на конструкцията няма да бъде нарушена.
Качеството на заваръчните съединения се влияе от много фактори: способността на материала да създаде монолитен шев, добавки и флюси, окисляемостта на метала, положението на шева: хоризонтален, вертикален, наклонен или таван.
Свойствата на заварката се определят главно от нейните геометрични размери.
Общи геометрични параметри:
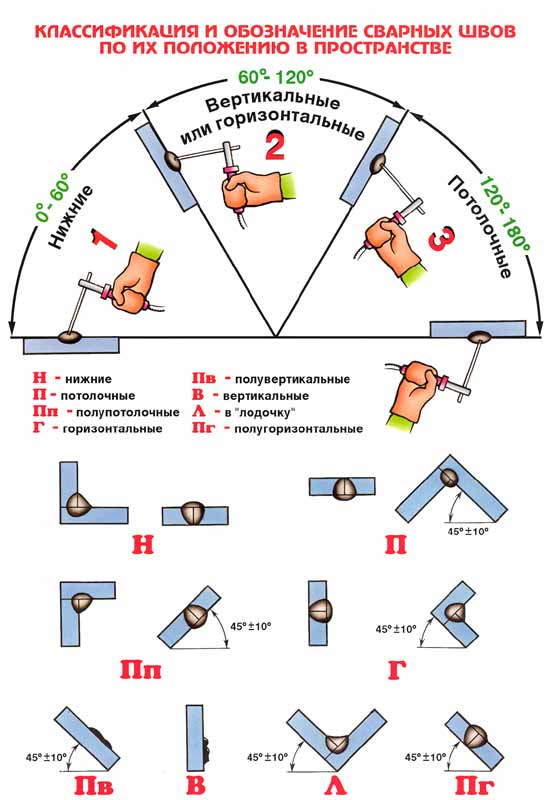
Класификация и обозначаване на заваръчни шевове.
- Ширина - разстоянието между границите на синтеза.
- Вдлъбнатост (изпъкналост) - разстоянието между линията и основния метал и повърхността, визуално преминаваща по линията на максималната вдлъбнатост (изпъкналост).
- Коренът е най-ниската част.
За ъглови съединения са характерни и следните стойности: наличие на крак на заварка, дебелина, изпъкналост и проектна височина.
Кракът на ъгловия шев е крак на най-големия равнобедрен триъгълник, вписан в напречното сечение. При заваряване на заготовки със същата дебелина, кракът може да се постави по ръба, а ако е различен, се настройва според дебелината на по-тънкия материал. Размерът на крака трябва да гарантира здравината на връзката, но прекомерното му увеличаване може да причини деформация на продукта.
Важна е формата на повърхността на заварката: изпъкнала, вдлъбната или плоска. Шевовете с изпъкнала повърхност - подсилени - работят по-добре при статични натоварвания. Вдлъбнатите повърхности - отслабени - по-добре издържат на динамични натоварвания. На практика шевовете с плоска повърхност се използват по-често като по-универсални.
Допълнителни функции
Формата на повърхностите на шевовете зависи пряко от използваните електроди.
В допълнение към общите изисквания за всички произведени електроди (постоянен запалване на дъга, определен химичен състав на заваръчния метал, без пръски и др.) Също се налагат специални изисквания. Те включват получаване на шев с определена форма. Електродите, чиято стопилка дава плътна и вискозна маса, лесно образуват изпъкнал шев.
Изборът на електроди се извършва в съответствие с техническите характеристики, посочени на всяка опаковка, в съответствие със спецификациите, посочени в проекта.
Условията на заваряване влияят върху свойствата и геометрията на заварката.
С увеличаване на силата на тока, дълбочината на проникване се увеличава с постоянна ширина на заваряване. С увеличаване на напрежението ширината на шва се увеличава рязко с последващо намаляване на дълбочината на проникване. С увеличаване на скоростта на движение на електрода до 50 m / h, ширината на шева намалява и дълбочината на проникване се увеличава. Увеличаването на скоростта с повече от 50 m / h е ирационално, защото могат да се получат подрязвания поради лошо нагряване на основния материал.
Качеството на съединенията се осъществява по два начина: деструктивен и безразрушителен.
Неразрушаващи тестове ви позволяват да идентифицирате външни дефекти, използвайки специални заваръчни модели, вътрешни - чрез ултразвук, рентгеново предаване и гама-излъчвател.
Деструктивното изпитване се извършва чрез пробиване, изпитване на якостта на опън, огъване, ударна якост с разрушаване на пробите.